Siamo andati a trovare Flavio Covini, General Manager di Cober, una delle aziende leader in Italia nella produzione di bastoni da montagna, per farci raccontare come nascono i loro prodotti per lo sci e l’escursionismo.Fondata da Renato Covini nel 1953, a cui è succeduto il figlio Flavio negli anni ’90, Cober si è sempre contraddistinta per l’innovazione, nei materiali e nel design dei prodotti, ponendo nel tempo sempre più attenzione anche a una produzione basata su processi rispettosi dell’ambiente.
4Outdoor è anche su Whatsapp. È sufficiente cliccare qui per iscriversi al canale ed essere sempre aggiornati.
L’intervista a Flavio Covini, General Manager di Cober
Cober è oggi conosciuta per la produzione dei bastoni da montagna, ha operato anche in altri settori?
Dalla sua fondazione è stata specializzata nella produzione di questo tipo di prodotto ma fra gli anni ’60 e ’70 c’è stata una parentesi durante la quale sono stati sviluppati anche attacchi per sci da discesa e negli anni ’80 pure racchette da tennis, forcelle e telai per biciclette. Quindi, diciamo che gli articoli sportivi sono sempre stati oggetto delle nostre attenzioni, con un particolare focus sull’innovazione di prodotto.
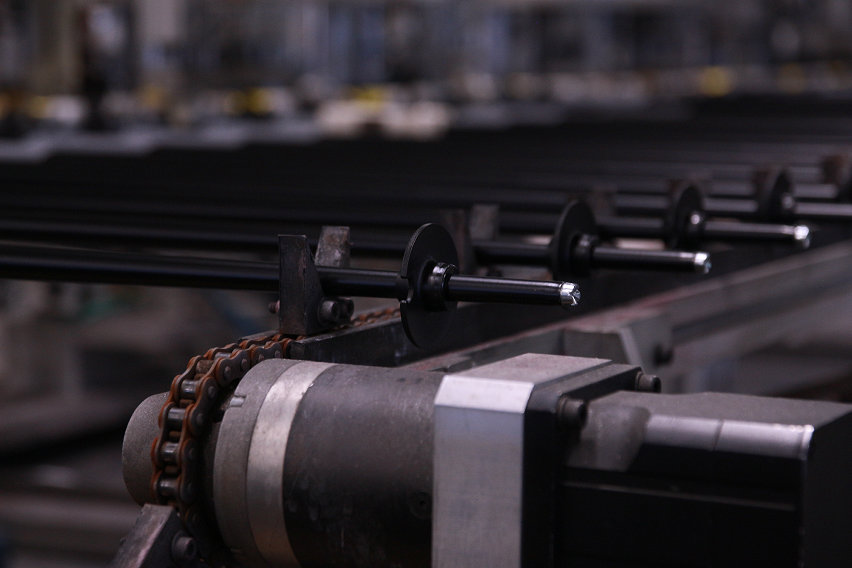
Quali step evolutivi hanno riguardato in generale i vostri bastoni da montagna?
Beh, l’evoluzione di questo prodotto è stata continua negli anni, a partire dai materiali, e se dal legno negli anni ’50 passammo all’acciaio, già negli anni ’60 questo veniva da noi soppiantato con l’alluminio, un materiale più leggero e che può, per esempio, essere colorato con qualsiasi tinta. Un’altra innovazione ha riguardato le manopole che sono passate in quegli anni dall’essere realizzate in gomma alla plastica, materiale che ha consentito di disegnare modelli ergonomici. La plastica, inoltre, è arrivata a essere utilizzata anche per la produzione delle rotelle, che in passato erano uno degli elementi di maggior peso.
Hai parlato di alluminio, alluminio colorato. Come lo colorate, per anodizzazione?
No, non usiamo questo metodo, per adottare questo procedimento in Europa bisogna che l’azienda in oggetto si doti di un sistema di smaltimento delle scorie, perché è un processo molto inquinante, di conseguenza è molto costoso. Per questo motivo l’alternativa che adottano alcune aziende è far produrre in Cina, dove le normative sono diverse. Noi però coloriamo attraverso la verniciatura a polvere.
L’evoluzione del bastone da montagna è stata continua negli anni, a partire dai materiali, e se dal legno negli anni ’50 passammo all’acciaio, già negli anni ’60 questo veniva da noi soppiantato con l’alluminio
Flavio Covini, General Manager Cober
Il tubo di alluminio lo producete voi?
No, i tubi si ottengono partendo da una piattina di alluminio che poi viene arrotolata, elettro-salda e tagliata.
A noi arrivano dal produttore queste scatole di tubi tagliati e registriamo a sistema tutte le informazioni di produzione del lotto. Tenere traccia di ogni passaggio della produzione non è molto comune nel nostro settore industriale, ed è costoso, ma consente anche a prodotto finito di risalire a ogni passaggio fino a individuare da quale lotto veniva il tubo. La stessa cosa avviene per la plastica che usiamo per manopole e rotelle, plastica che lavoriamo noi a partire dai grani acquistati dal produttore.
Tracciare tutta la filiera e procedere in modo sistematico al controllo qualità è una bella garanzia per il consumatore finale.
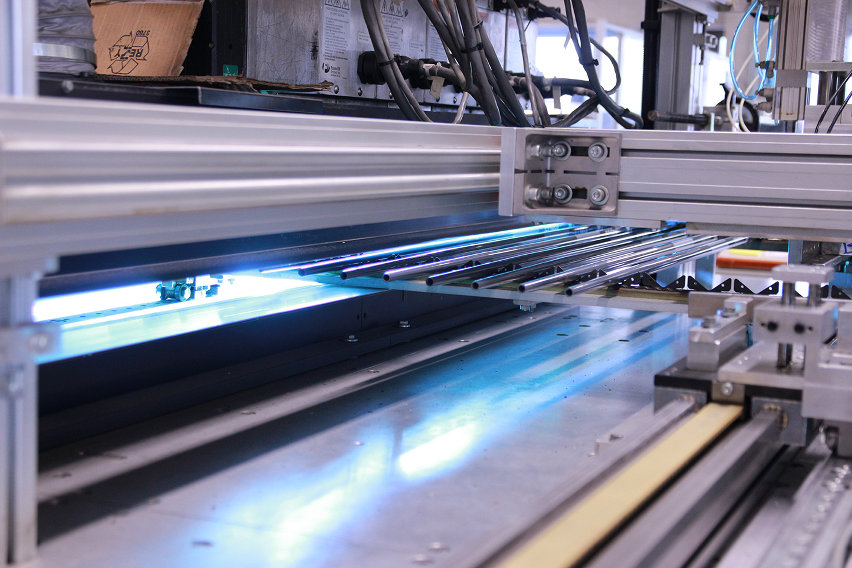
Siete certificati ISO?
No, non abbiamo la certificazione ISO 72, ma operiamo secondo lo stesso standard. A ogni passaggio produttivo i nostri operai registrano su un form tutti i parametri di lavorazione e la provenienza del semilavorato.
Tornando all’alluminio, che lega utilizzate?
Abbiamo due fornitori di tubi in alluminio, entrambi europei, e le leghe che utilizziamo sono la 50-83 per i prodotti entry level, mid range, e la lega aeronautica 70-75 per quelli di alta gamma. Quest’ultima, per dare un’idea, ha una resistenza di 42 kg/mm2.
Mi dicevi che i tubi che vi arrivano hanno una sezione cilindrica, come li lavorate?
Sì esatto, i tubi ci arrivano cilindrici, ma i bastoncini hanno diametri di sezioni diverse alle due estremità. Per modificare la loro sezione usiamo delle macchine chiamate martellatrici.
Queste macchine, ne abbiamo 5, hanno al loro interno degli stampi (con la forma conica in negativo) che martellano letteralmente il tubo per cambiargli forma.
I tubi con lega 50-83, dopo che sono stati modellati in forma conica, vengono leggermente scaldati e poi sono pronti per lavaggio e verniciatura. Al contrario, quelli in lega 70-75 devono essere temprati perché fino a quel momento non hanno la durezza desiderata, sono “morbidi”.
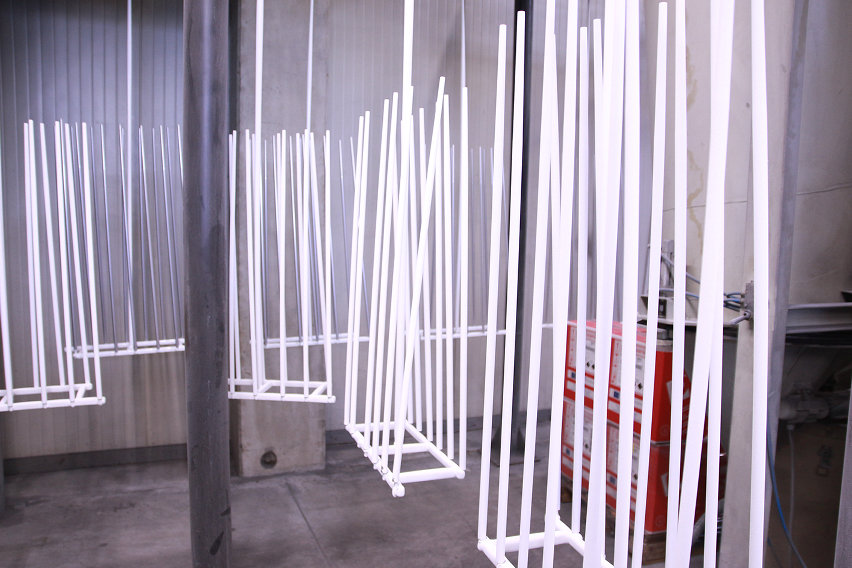
Il processo di tempra si articola in tre fasi distinte: la tempra vera e propria, la raddrizzatura e l’invecchiamento.
La tempra dei tubi avviene in forno per 4 ore a 380 – 450°C, poi questi vengono raffreddati con acqua. A quel punto però si saranno anche stortati e devono passare per la raddrizzatrice. Successivamente fanno ancora un passaggio in forno a 120° C per 24 ore, raggiungendo la durezza massima, che ci premuriamo di controllare a campione.
Non abbiamo la certificazione ISO 72, ma operiamo secondo lo stesso standard. A ogni passaggio produttivo i nostri operai registrano su un form tutti i parametri di lavorazione e la provenienza del semilavorato.
Flavio Covini, General Manager Cober
Una volta che il tubo ha ottenuto la forma e la durezza desiderata, cosa succede?
Dopo le lavorazioni sopracitate, il tubo è ancora grezzo (sporco dalla lavorazione) ed entra in un impianto di lavaggio che utilizza il metodo della fosfatazione, una soluzione a grandi linee di acqua e sapone in impianto chiuso che ricircola il liquido. Poi, una volta che il tubo è stato lavato e risciacquato con acqua demineralizzata, entra nel forno per circa dieci minuti.
La catena di montaggio lo porta quindi all’impianto di verniciatura.
I tubi vengono verniciati a polvere. In pratica il processo prevede il fissaggio del forno a terra, questo ha una carica negativa, mentre la vernice in polvere (che compriamo da un fornitore e versiamo nei serbatoi dell’impianto) è a carica positiva. Quando gli ugelli dell’impianto spruzzano la vernice sui tubi, la differenza di carica fra polvere e tubo fa sì che la vernice si aggrappi a esso. La polvere in eccesso viene aspirata e riciclata, quella in esubero viene raccolta e poi smaltita.
Una volta che il tubo è verniciato, fa un passaggio nel forno a 180°, 200°C per circa 2 minuti, in modo che la vernice catalizzi.
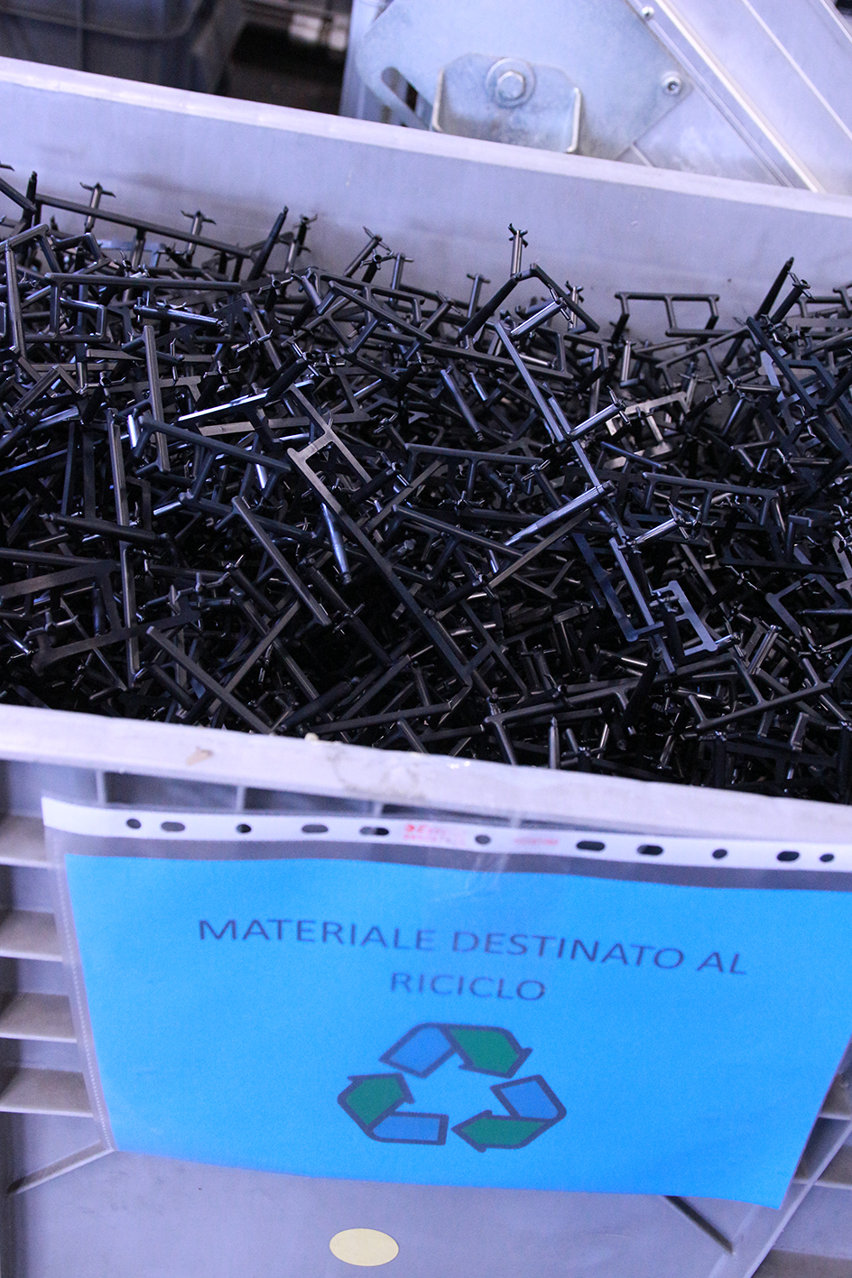
I procedimenti per decorare i tubi poi sono la serigrafia e il trasferimento da carta.
Il processo serigrafico avviene attraverso il rotolamento del tubo al di sotto del telaio di stampa. Lì viene a contatto con l’inchiostro, che non catalizza attraverso l’evaporazione dei solventi tramite calore, ma con i raggi UV, un processo più rapido ed ecologico, in quanto le lampade (oggi a led) producono solo ozono che viene aspirato.
Nel trasferimento dell’inchiostro da carta, il processo avviene per sublimazione. A una temperatura di 580°C l’inchiostro passa dallo stato solido allo stato aeriforme e si trasferisce per evaporazione nella base verniciata del tubo.
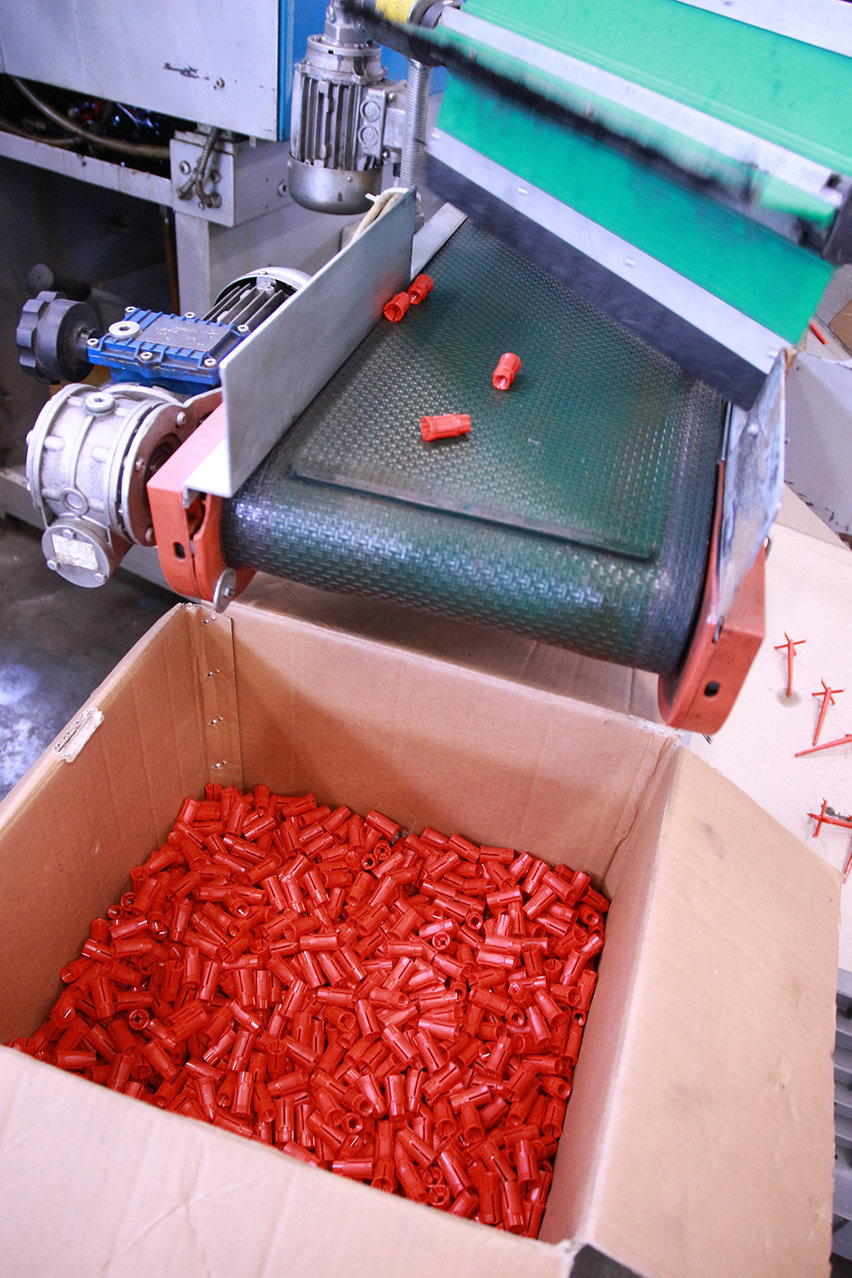
Nel trasferimento di colore da carta ci sono dei limiti relativamente ai colori?
Gli unici limiti sono che non si può trasferire il colore bianco, quindi occorre verniciare il tubo con una base di bianco, e che sopra il bianco bisogna dare una mano di trasparente, oppure il colore, trasferendosi sul bianco, si altererà a livello di tinta.
Il bastone, oltre alla struttura in metallo, ha delle componenti in plastica, come le producete?
La plastica (polipropilene) ci arriva in grani da un fornitore e viene miscelata al colorante. La macchina scalda il polipropilene attraverso delle resistenze e il sistema a iniezione alimenta lo stampo, che darà vita all’accessorio desiderato. Alcuni di essi non sono al 100% in plastica, ma sono prodotti con due materiali, in questo caso si faranno allora due iniezioni: una di plastica e una di gomma.
C’è uno scarto della lavorazione?
Sì, il materiale di scarto viene riutilizzato per esempio per fare gli allaccia-bastoni.
Ora abbiamo il tubo verniciato e decorato, e gli accessori in plastica. Come combinate i due elementi?
In Cober abbiamo un macchinario, un robot, che in diverse fasi, mentre fa passare il tubo, va a prendere la rotella, la manopola e il puntale e li fissa con una punta di colla in una posizione ben definita, riconosciuta da un sistema ottico.
Quanti bastoni producete al giorno?
La nostra produzione è di circa 2.000 bastoni al giorno, e può arrivare a 5.000 se facciamo anche il turno di notte.
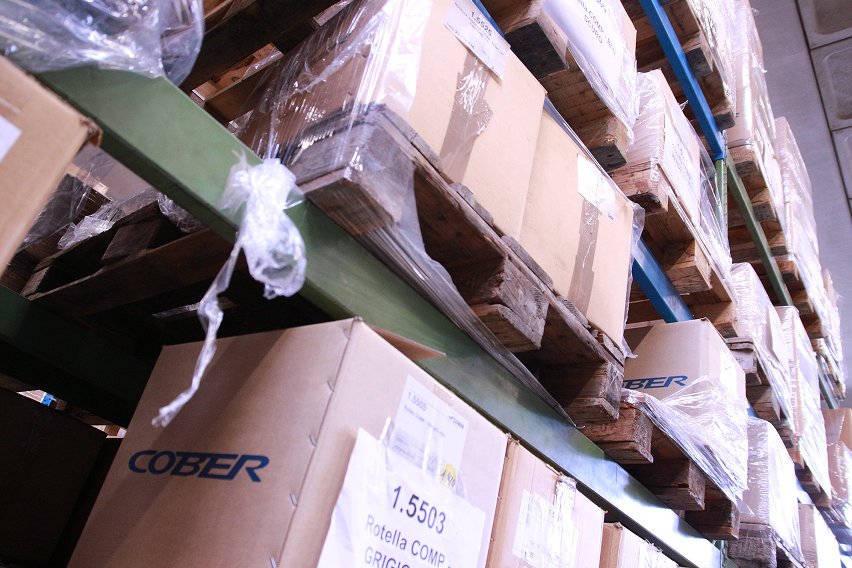