Il processo di creazione di un nuovo casco per il ciclismo spiegato con l’aiuto di Met Helmets, marchio italiano che ha sempre messo in primo piano la tecnologia e il design al servizio della sicurezza oltre che allo stile e le funzionalità.
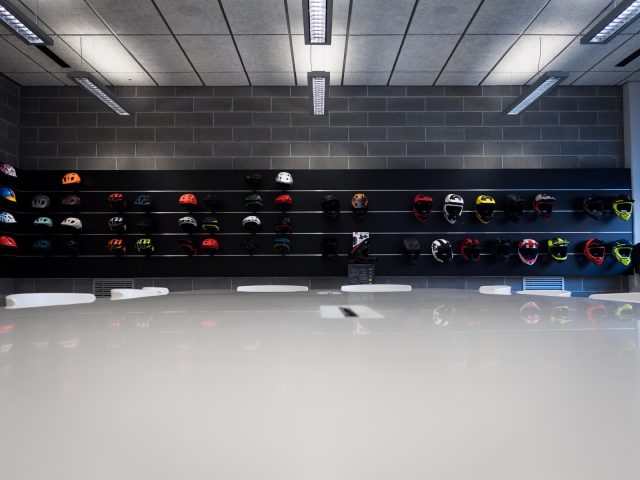
Fondata sulle rive del Lago di Como, da Luciana Sala e Massimo Gaiatto nel lontano 1987, la sede di Met Helmets si trova ora nel cuore delle Alpi a Talamona, in provincia di Sondrio. La struttura all’avanguardia è in grado di progettare, sviluppare e testare caschi dedicati a ogni disciplina del ciclismo in un singolo sito. In Met sono tutti orgogliosi di questo, consentendo loro di innovare e sviluppare nuovi prodotti in modo molto più rapido rispetto ai concorrenti principali.
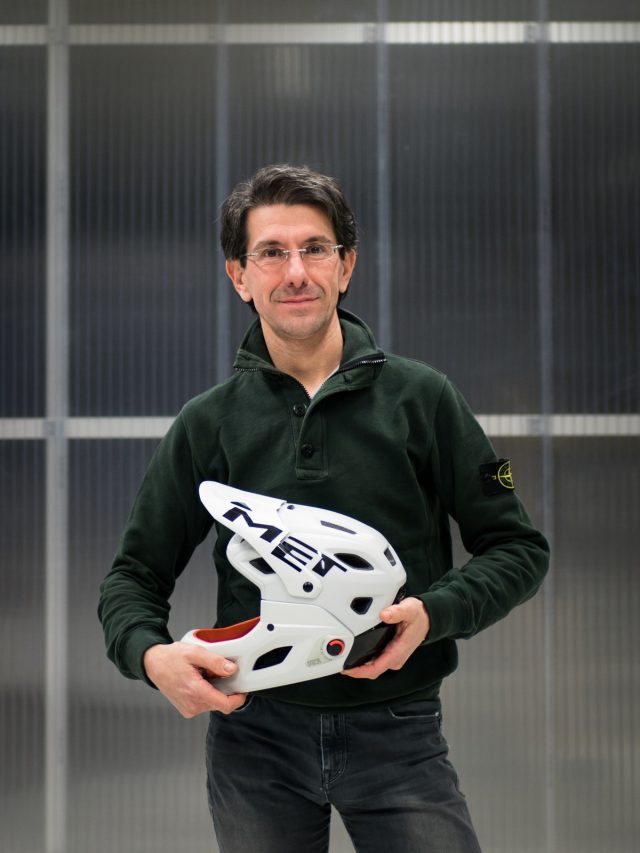
Dagli schizzi a mano al CAD
Il processo di creazione inizia naturalmente con i primi schizzi, lasciando al designer la massima libertà nel suo essere creativo.
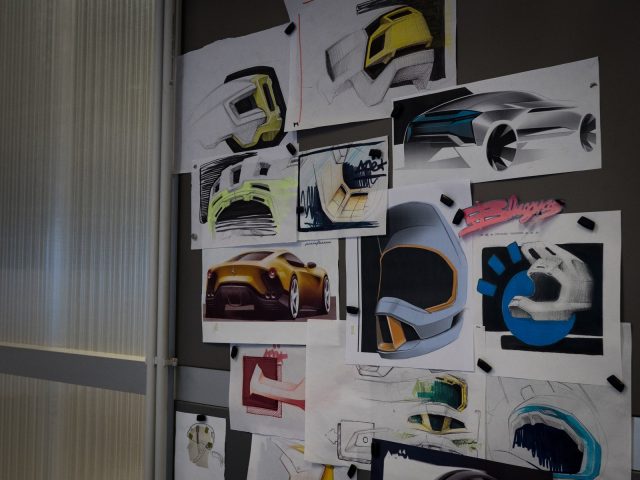
Dopo il raggiungimento del primo passo, si passa direttamente alla modellazione del casco attraverso il Computer Aided Design (CAD). È qualcosa di diverso dalla tecnica tradizionale, dove si modella l’argilla. Questo significa scansionare prima il modello in argilla, fare i primi campioni, e poi eseguire i test sulla resistenza agli impatti. Questo significherebbe anche aggiustare i materiali e la struttura dopo il test.
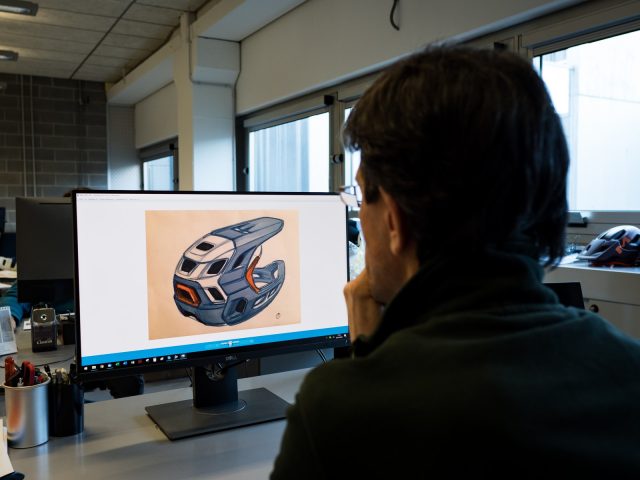
Passando direttamente alla progettazione CAD (un processo utilizzato da parecchi anni), Met può eseguire la simulazione virtuale dell’impatto, quelle relative alla gestione del calore, le simulazioni aerodinamiche, ma anche lavorare sulla forma interna del casco prima di avere in mano il primo campione reale. È un grande vantaggio perché, quando arrivano i primi esemplari, si sa già come si comporterà il casco. Questo significa che si potrà mettere a punto il casco e i materiali quando si avranno in mano i primi campioni.
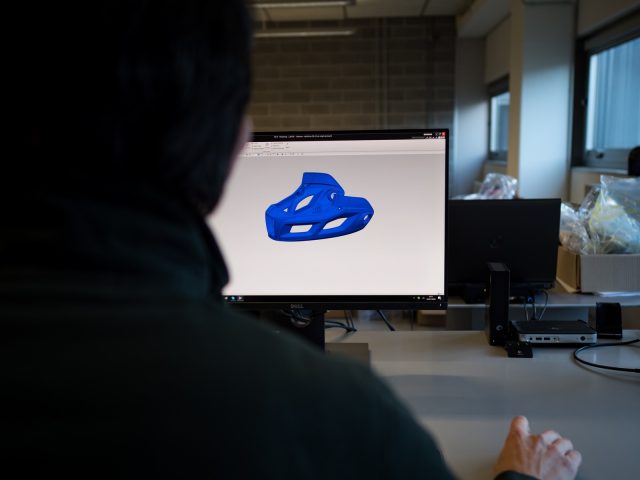
Nella fase CAD si lavora a stretto contatto con i partner, per esempio per integrare il sistema di protezione supplementare MIPS o per sviluppare caratteristiche esclusive come il meccanismo MCR con Fidlock (per il casco Parachute MCR con mentoniera rimovibile).
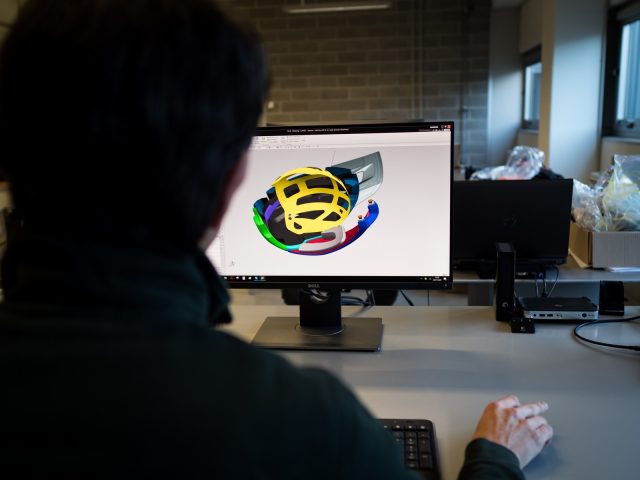
Stampa 3D
Dopo la modellazione 3D, arrivare la fase della stampa 3D: si stampano i primi campioni in scala 1:1 per vedere come sarà il casco.
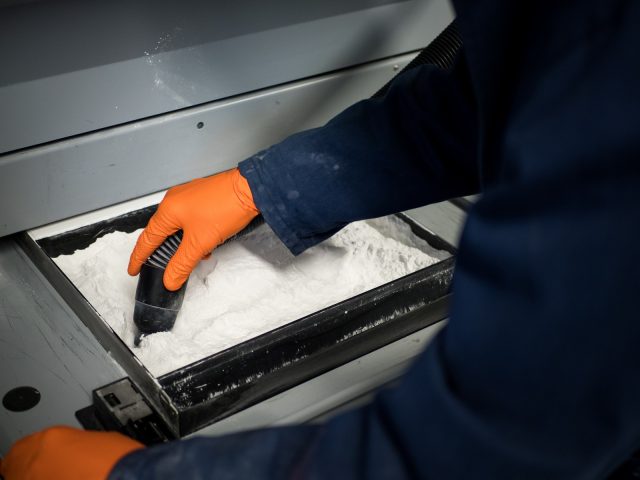
C’è la prima prova di vestibilità, anche se i campioni realizzati con la stampa 3D sono un po’ pesanti (notate la differenza tra il primo prototipo del Parachute MCR con la versione definitiva). È anche possibile stampare tutti i piccoli meccanismi e le parti più minuscole per validare l’integrazione, l’aspetto e ogni dettaglio. In questo modo si guadagna molto tempo prezioso.
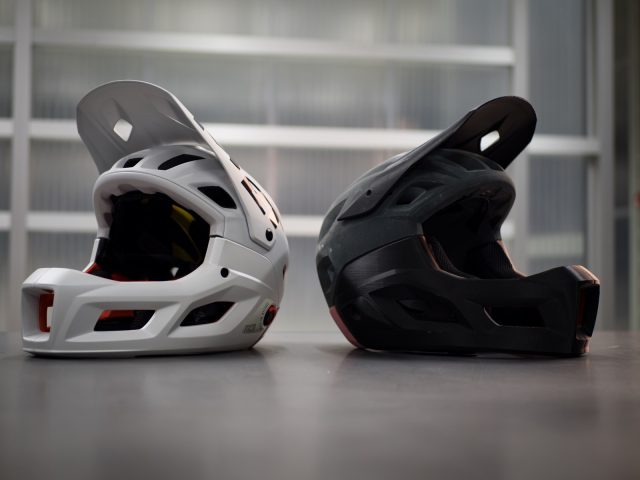
Quando la stampa 3D ottiene l’approvazione, vengono realizzati i primi campioni “reali” presso lo stabilimento proprietario in Cina, poi spediti alla seda principale italiana. Questi campioni sono utilizzati per confermare la simulazione degli impatti effettuati in precedenza al computer. Ma anche per mettere a punto il casco, convalidare la calzata e il design, calibrare la produzione, approvare i colori e le grafiche, e infine eseguire i primi test interno nel proprio laboratorio.
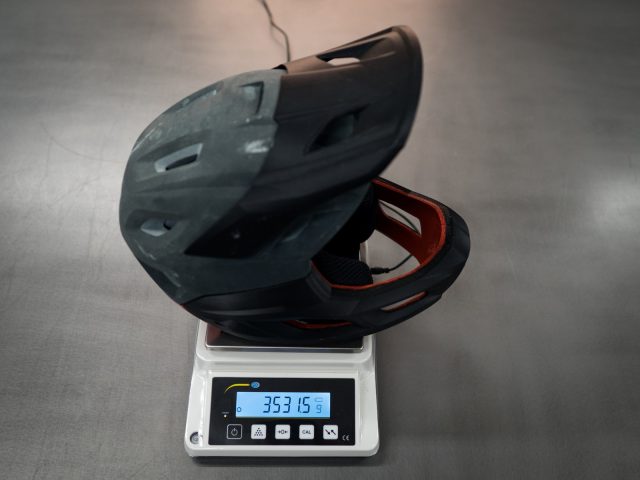
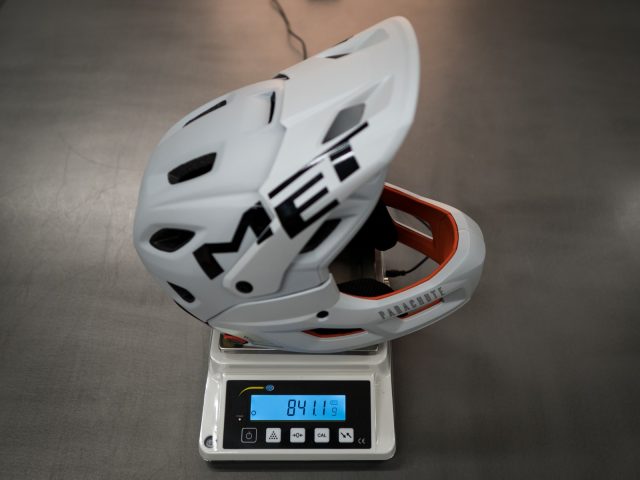
Laboratorio interno
Met Helmets è uno dei pochi marchi al mondo ad avere una struttura di test completamente attrezzata all’interno del proprio laboratorio.
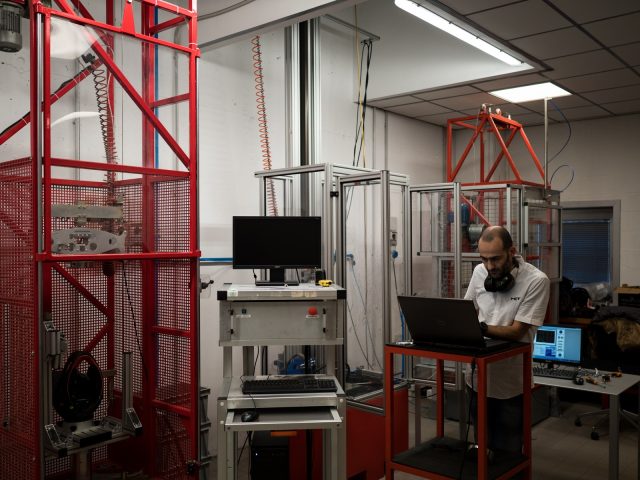
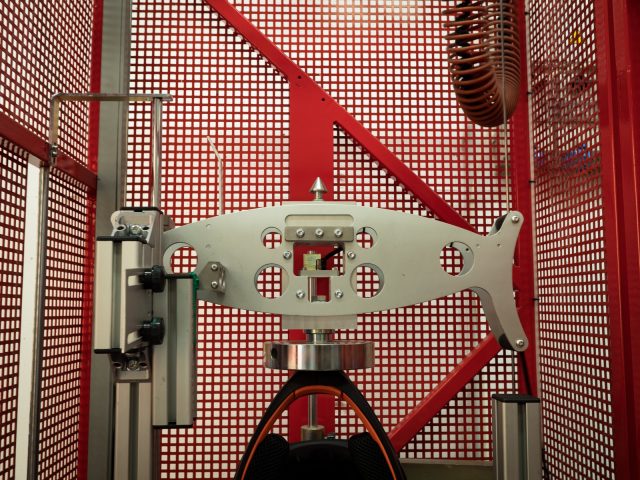
È possibile simulare qualsiasi tipo d’impatto, sia seguendo gli standard di certificazione, sia eseguendo test interni più stressanti. Non manca un’attrezzatura di prova per eseguire le prove di impatti rotazionali, quelli tanto cari alla tecnologia MIPS.
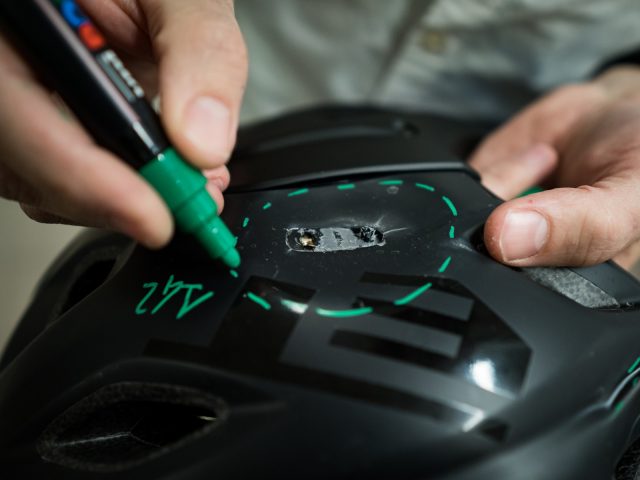
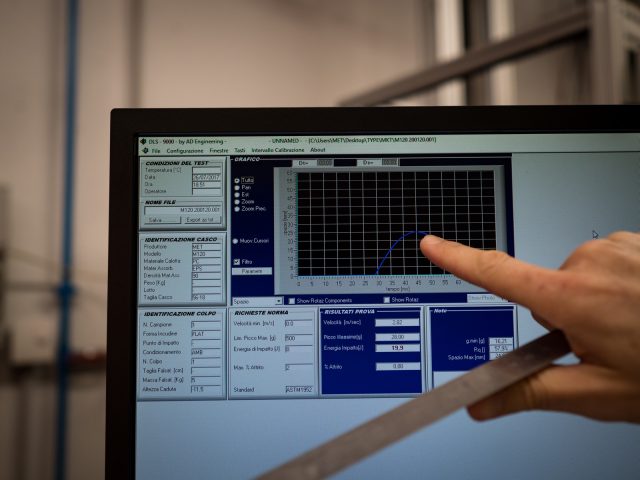
Questo permette di eseguire una grande quantità di test assolutamente indispensabili per raggiungere la massima sicurezza. Per fare un esempio, Met esegue 700 impatti sul modello Legit Carbon da gravity prima che venga inviato al laboratorio dedicato alla certificazione ufficiale (il che significa più di 140 caschi distrutti). È un qualcosa che non puoi fare senza avere un laboratorio e interno e dipendenti dedicati a questo delicato compito.
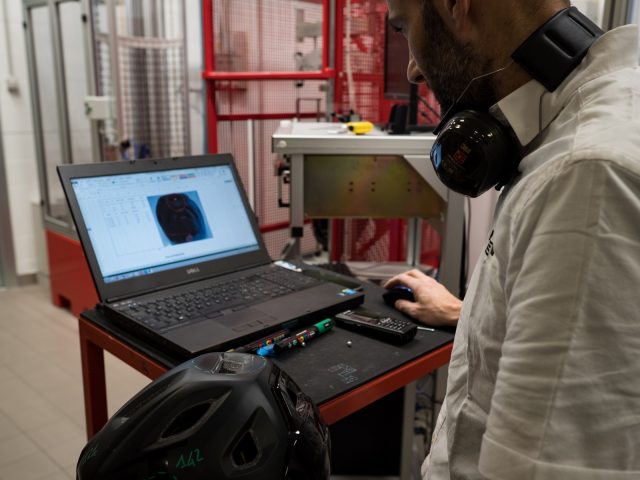
Certificazione ufficiale
Poi il casco viene inviato al laboratorio indipendente per essere certificato secondo le principali normative vigenti: CPSC (USA) | CE | AS/NZ. Questo include anche ASTM o NTA a seconda dei modelli. Si tratta di certificazioni non obbligatorie, ma molto importanti. Infatti ASTM è l’unica che garantisce la sicurezza della mentoniera, fondamentale per i modelli full face da gravity (DH/Park Riding) e per quelli convertibili da Enduro.
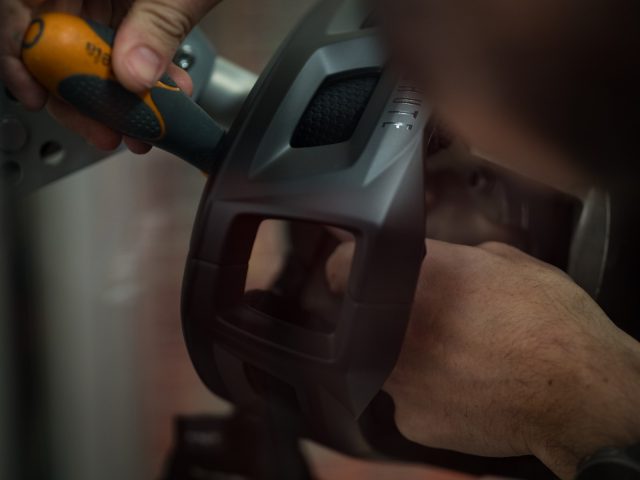
La produzione finale
Finalmente si arriva alla produzione. Questo non rappresenta la fine dei test, perché Met esegue una serie di prove a campione su ogni lotto di produzione presso il proprio laboratorio interno, che offre opportunità illimitate di accrescere le proprie conoscenze sulle conseguenze degli impatti.
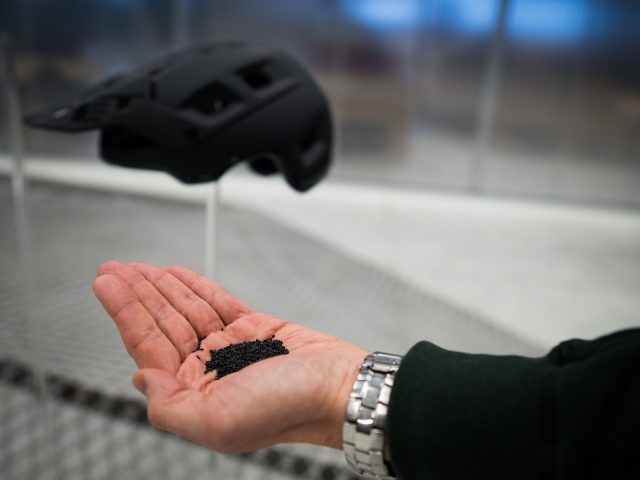
Una cosa che si può dire di Met Helmets è che ha una grande conoscenza nel campo nella produzione: crea caschi per il ciclismo da più di 30 anni, costruendo un’esperienza da leader nel settore con più di 25 anni di produzione interna. Il marchio lombardo ha personale italiano nelle fabbriche all’estero, con gli ingegneri che visitano spesso gli stabilimenti con cui sta lavorando in Cina, per controllare e seguire il processo di formazione del personale.
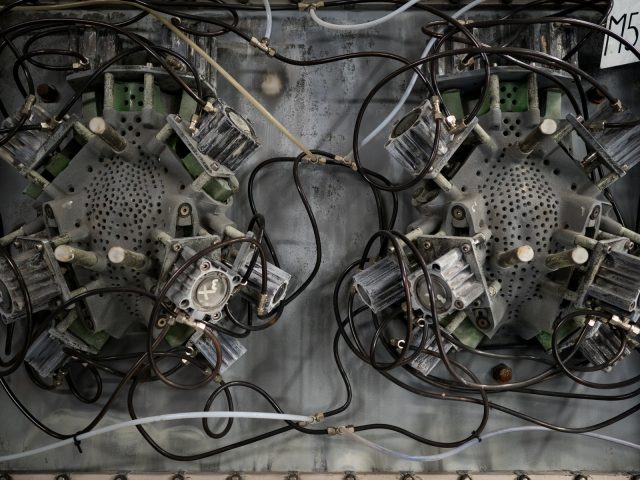
Essere specializzati in caschi ma anche in protezioni – con il marchio Bluegrass – è un grande vantaggio perché permette di dedicarsi realmente al 100% alla realizzazione del miglior prodotto possibile per ogni tipo di biker: road, MTB, city, eBike, e anche bambini.
Info: Met Helmets
[Foto: Ulysse Daessle/Met Helmets]